Business intelligence for transportation companies is a process of end-to-end analysis of past and current events aimed at collecting valuable data for strategic decision-making. BI tools process huge amounts of data from various sources and provide results in user-friendly formats. Today, business intelligence is becoming a key tool for logistics companies to improve profitability. Every trucking company, whether it is an individual entrepreneur with three cars or Rosneft with an armada of many thousands, will always have a few directions for automating processes and reducing costs.
In the period of sanctions and economic crisis, car business owners more than ever want to know - what money is spent on, where failures occurred, how to increase the profitability of the enterprise. And if you have monitoring data, it means you manage the fleet!
How it used to be counted
In the early 2000s, at the dawn of the era of satellite monitoring, the first vehicles began to be equipped with location trackers, fuel level sensors, terminals for processing and transmitting data to the control panel. Boxes with paper reports went to dispatchers, accounting, technical department and other services of the enterprise. Working with the same indicators, employees did not know what was going on in the neighboring office. As a result, the management received “crooked” calculations, in which the picture of the business fell apart into small puzzles. As a consequence: non-transparent cost items, falling margins, excess or lack of stocks of consumables, fuel and lubricants, vague data on profits, invisible weaknesses in production, lack of understanding of where to go next.
Modern digital fleet management solutions
The fourth industrial revolution at trucking companies is when the owner of a corporation receives not a set of hardware and instructions, but a full range of services and competencies that can fundamentally change the style of production management and increase the economic effect. The head of the company, being on vacation or on a business trip anywhere in the world, receives full information about the work of his fleet in one click. This allows top managers to draw the right conclusions and make effective management decisions. In Russia, a comprehensive solution MONTRANS.ANALYTICS has been developed, which combines data on tens of thousands of vehicles and special equipment, helping clients to make the process of managing transportation companies transparent and convenient.
Initially, many IT solutions based on the 1C platform were oriented, first of all, on accounting for the majority of activities of enterprises. Such developments provided management with tools to generate reports in manual mode. Such a system is also called “descriptive analytics”. Today in large companies there is a trend for transition to the so-called “deep analytics” and obtaining top-level reports.
How can analytics be bolted on to a bulldozer?
After integrating the analytical platform into the enterprise management system, the savings of resources and time will be noticeable after a month of using the analytical service. For example, the dispatcher of a mining plant will know not only where the bulldozer was located, how much fuel it was filled with, but also how long the machine worked with the blade lowered, what part of the working day the driver was idle, how much fuel was wasted. Such statistics is collected for each piece of equipment. The manager receives a final report, thanks to which it becomes immediately clear - who is working and who is making an appearance.
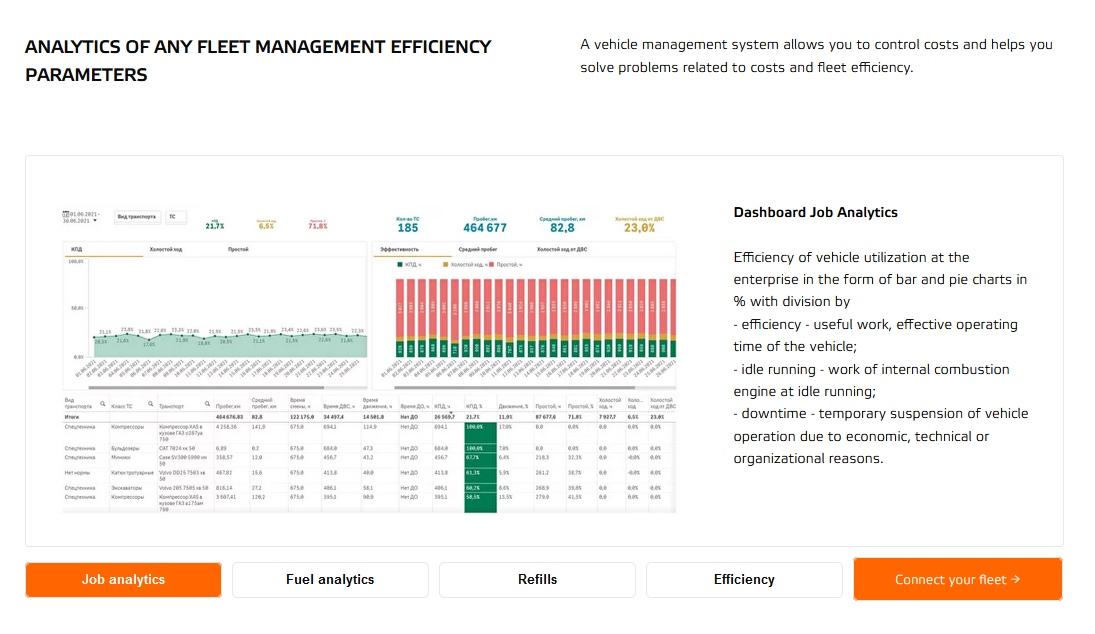
The overall efficiency of a cloud service is made up of factors such as:
- Reduced database processing time;
- Reduction of paperwork;
- Reduction of fuel and lubricant costs;
- Reducing the time of idle running of vehicles;
- Increase in efficiency of equipment utilization;
- Reduction of repair and spare parts costs;
- Rational use of storage resources;
- Efficient placement of vehicles on objects;
- Reducing the number of accidents;
- Improved employee driving culture;
- Reduction of time for decision making;
- Possibility to forecast business development.
Evgeny Maksaev, managing partner of “MONTRANS”: “The profit of the enterprise directly depends on how effectively the fleet management manages resources and uses monitoring data. MONTRANS.ANALYTICS program service allows to significantly reduce fuel and lubricant costs and increase the productivity of each unit of equipment. The business intelligence system of transportation companies simplifies the tasks of technical and financial administration by combining the entire huge amount of data within one management standard. As a result, management receives top-level reports with absolutely reliable indicators, as their preparation was not influenced by the human factor. Diagrams, graphs and summary tables provide complete information on the operation of all vehicles. Under control: movement of vehicles, time of work of vehicles, refueling, work of mechanisms, idle time, motor-hours, traffic violations and many other parameters. As a result: MONTRANS.ANALYTICS solution increases the efficiency of machinery and economic efficiency of the fleet.”
Hard, but necessary
In Russia, as well as in CIS countries, business process analytics is still perceived by many managers as something exorbitant and expensive. Fleet owners have not even tried to calculate the ratio of money invested in digitalization to the practical benefits of business analysis. Some top managers do not want to understand that the use of analytical services in transportation provides instant access to various databases. Within a day, the system collects and integrates several billion metrics on which analytical conclusions are based. The IT solution produces more than 30 reports containing various parameters. The cloud platform fundamentally changes the fleet management system, showing real costs, bottlenecks and areas for improving business efficiency.
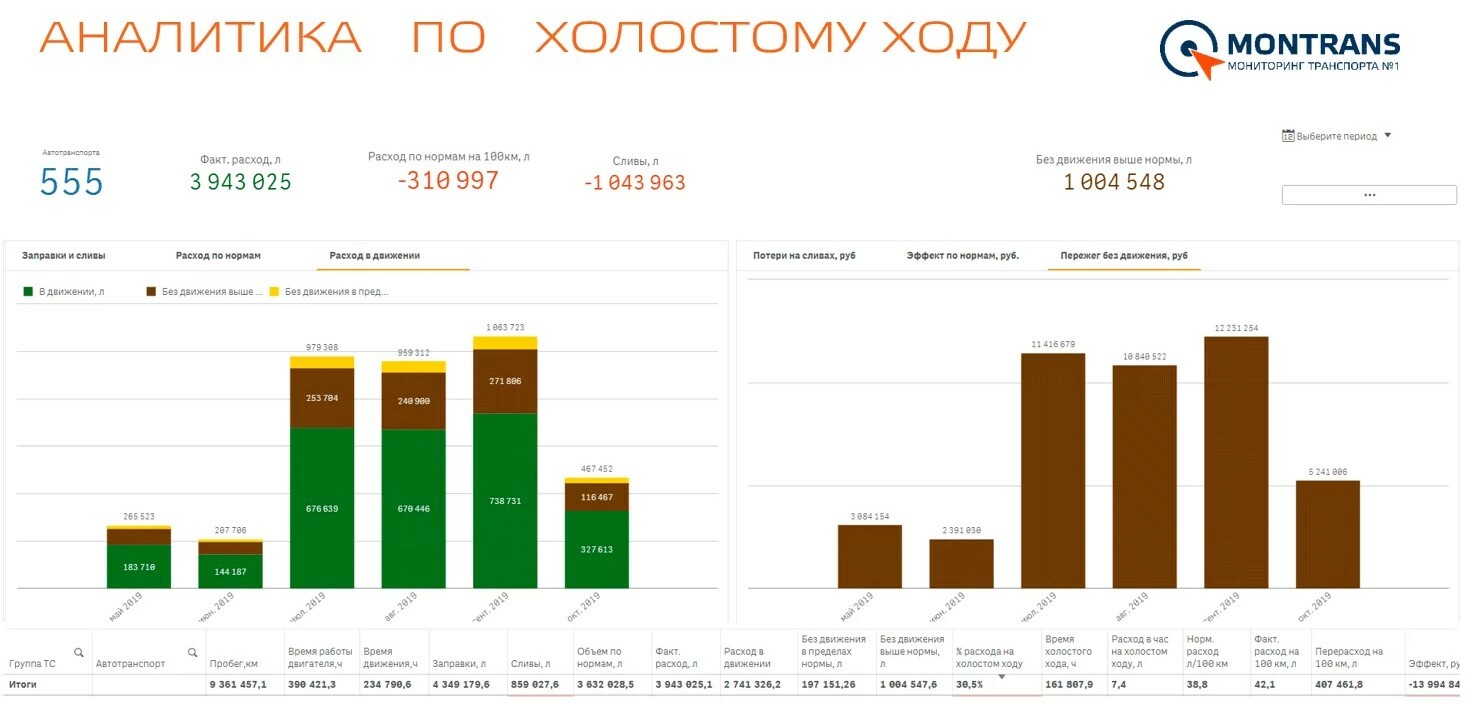
According to experts of MONTRANS Group, in more than 70% of cases, having started the digitalization of the fleet, the management does not bring the matter to the end and does not calculate the lost profit. This may be due to the fact that resources may have been diverted to another project. And sometimes management competencies ran out during the implementation phase when new issues arose. However, where deadlines, goals and executors were clearly set, business owners summarized positive results. For example, at Yakovlevsky Mining and Processing Plant (Severstal PJSC), as a result of MONTRANS.ANALYTICS implementation, they outlined a program to increase transport efficiency and during six months every month increased it by 3%. They also achieved a 70% reduction in the accident rate thanks to the introduction of the MONTRANS DVR intelligent driver monitoring and assistance system. And in the company “KVS International”, after the integration of business intelligence, they achieved a twofold increase in the service mileage of vehicles and fuel savings of 30%. According to the management of these companies, the installation of the intelligent control and enterprise management system paid for itself in the first year of operation.
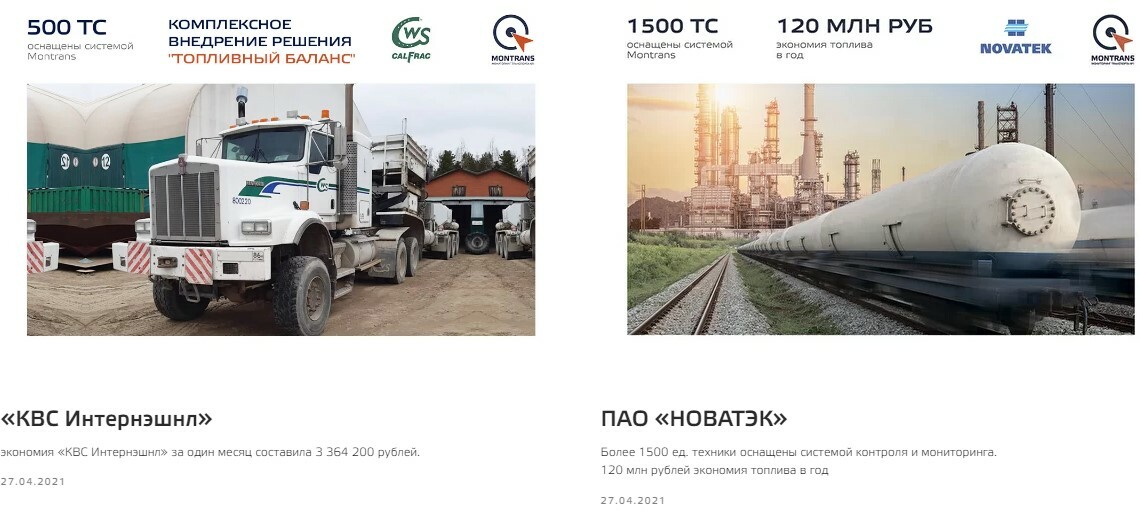
Dmitry Zhuravlev, Managing Partner of MONTRANS Group of Companies: “We are now living in the era of the fourth industrial revolution. And we already know what “Revolution 5.0” will be. Today, cloud technologies manage humans and help them correct mistakes. This minimizes the human factor. As one of our customers stated: “Where are we going with our carpool to your digital world?”. To which we replied: “If you don't try to change, you can remain a car depot for the rest of your life.